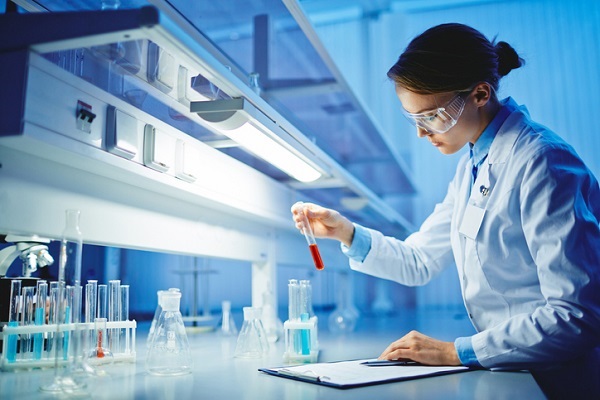
Young woman working with liquids in glassware
Introduction to Quality Control in Pharmaceutical Industry
Think About This: Would you prefer a drug that can cure all your sicknesses and give you comfort and happiness for the rest of your life but reduce your life span a bit, or would you go for the one that will manage your sickness a bit with discomfort and unhappiness but gives you long life? If you can attempt this question, then understanding Quality control in pharmaceutical industry won’t be difficult for you.
Imagine This Too: You pick up your prescription medication from the pharmacy trusting that it will help you cure your illness so you can be fit, healthy and happy again. But what if that drug was not properly tested for quality? The consequences could be life threatening.
Quality control in pharmaceutical industry ensures that every pill, injection, or ointment meets stringent standards for safety and effectiveness. In this article, we’ll explore everything you need to know about this critical process.
In this expository and explanatory article, you will learn the following:
- What Quality Control in the Pharmaceutical Industry is.
- The main goals of Quality Control in Pharmaceutical Industry.
- The importance of Quality Control in Pharmaceutical Industry.
- Key components of Quality Control in Pharmaceutical Industry.
- Quality Control Techniques and methods.
- Regulatory Standards and Guidelines..
- Roles of quality control professionals.
- Skills to master as a quality control personnel.
- How to land high paying job as a quality control personnel.
What is Quality Control in Pharmaceutical Industry?
The answer to the questions in the first two paragraph above explain what quality control is in pharmaceutical industry. For the sake of clarity, we will define the keywords individually.
What is quality? Quality as defined by oxford is “the standard of something as measured against other things of a similar kind; the degree of excellence of something.” Additionally, it is also defined as “a distinctive attribute or characteristic possessed by someone or something.”
From our definitions above, we can say that quality is simply excellence. If perfection becomes too difficult to achieve, the lowest any pharmaceutical company that love quality can fall is excellence. Anything that is below excellence lacks quality.
What is control? According to Oxford, control is “the power to influence or direct people’s behaviour or the course of events”. It also defines it as “a person or thing used as a standard of comparison for checking the results of a survey or experiment.”
Wikipedia defines the pharmaceutical industry as “an industry involved in medicine that discovers, develops, produces, and markets pharmaceutical goods for use as drugs that function by being administered to patients using such medications with the goal of curing and/or preventing disease”.
Simply put, quality control (qc) in pharmaceutical industry controls the quality of a pharmaceutical product. It is the implementation of mechanisms, programs and tools for product improvement and assurance.
Quality control personnel/professionals are tasked with the responsibility of ensuring that every pharmaceutical product meet specific standards before and even after they are released into the marked.
It is a crucial process to ensure that high quality pharmaceutical products are consistently produced following standards established by regulatory bodies. This process ensures that products meet standards appropriate for their intended use.
What are the main goals of Quality Control in Pharmaceutical Industry
The goals of quality control in pharmaceutical industry is enormous. The most obvious of them is the fact that quality control in the pharmaceutical industry thrive to safeguard the life of the masses who are the end users of the pharmaceutical products. However, to achieve this, other important main goals must be achieved.
Let’s look at these main goals of quality control in pharmaceutical industry
Product Safety, Efficacy and Quality
A major goal of quality control in pharmaceutical industry is to ensure product safety. The lives of the public are in danger if a pharmaceutical company fails to establish a quality control department in the organisation.
By ensuring product safety, efficacy and quality, qc can safeguard the life of the end users of pharmaceutical products. This will boost the confidence of both the manufacturers and end users of the drugs. More so, a company that has a working quality control department with qualified professionals can boast of their products anywhere in the world.
Simply put that qc gives the pharmaceutical industry confidence by ensuring that the products the companies produce meet the required standards.
Quality control in pharmaceutical industry ensures product safety by carrying out rigorous analysis on raw materials, equipment, tools, intermediate and finished products. These analysis are important to ensure that the equipment and tools intended for use for pharmaceutical manufacturing will consistently produce high quality products that meet the set standards.
They test raw materials to ensure that they are fit for production by checking if they are actually what they are claimed to be.
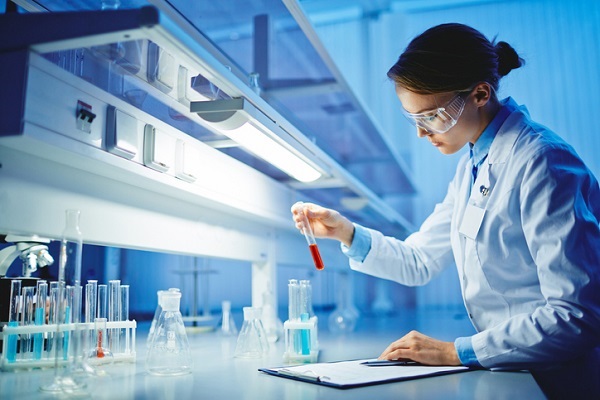
More so, they test intermediate and finished products to ensure that quality is maintained before, during and after production. It is extremely important to ensure that pharmaceutical products do not contain any trace of toxic substances. This is what qc does.
Additionally, they test stability samples and carryout post market survey to monitor the stability of their products. All these are done to ensure that quality is maintained at all time while prioritising the lives of the end users.
Compliance with Regulatory Standards
Quality control ensures that all manufacturing processes and products comply with regulations set by national and international authorities such as the FDA, EMA, NAFDAC, WHO, etc depending on the country.
All pharmaceutical manufacturing processes must follow one or more regulatory standards like Current Good Manufacturing Practices (cGMP), Good Laboratory Practices (GLP), etc. These standards are overseen by regulatory bodies that make the standards.
For instance, production processes, methods, analysis and even equipment must comply with some specific regulations. Quality control ensures that there are no deviations from these standards.
Protecting Consumer Health
This is the major goal of quality control in pharmaceutical industry. Every other goals aim to achieve this.
QC ensures patient safety by ensuring that all pharmaceutical products are safe for consumption and do not pose health risks to patients who rely on those products for quality health.
Quality control also engage in risk management to identify and mitigate any risks associated with the production and use of pharmaceutical products. Without quality control, the pharmaceutical industry will be wasting lives while trying to save them.
Enhancing Product Shelf Life
Quality control conducts stability testing to determine the shelf life of products and establish appropriate storage conditions. This is continuously monitored to ensure that products remain stable when stored at the appropriate storage condition.
Quality control also ensures that expiration dates are accurate and reliable.
Improving Production Processes
QC contributes greatly to the improvement of production processes by establishing quality initiatives to ensure product quality and production efficacy. It is the goal of quality control to improve production processes.
They usually engage in planning with the production team to see how they can better the production processes while maintaining or improving product quality.
Additionally, they engage in process validation to ensure that the manufacturing processes continuously produce high quality pharmaceutical products that meet the required internal and external standards.
The good thing about quality control is that their processes are reliable because all the analytical methods, equipment and even personnel involved in the process validation are also validated, calibrated, verified and qualified.
Ensuring Proper Packaging and Labelling
It is the goal of quality control in pharmaceutical industry to protect pharmaceutical products from damages. Pharmaceutical products are designed and packaged such that it can withstand some certain environmental conditions. QC ensures that these packages are durable and protects the products from damages.
They also ensure high quality packaging to protect the products and the company at large from counterfeiting, thereby protecting the company’s image and reputation.
Building Consumer Trust
It is in the interest of quality control that the end users of their pharmaceutical products have trust in their products and their brand at large. This is another good reason why they work hard to give the best quality products possible.
The importance of Quality Control in Pharmaceutical Industry.
The importance of quality control in pharmaceutical industry cannot be overemphasised. Quality control prevents pharmaceutical companies from deviating from regulatory standards. This helps the company to be free from regulatory sanctions caused by deviations.
Quality control is also very important in the pharmaceutical company because it ensures product quality and patient safety, building strong trust in the end users.
It also saves costs and time for the company by engaging in process validation to ensure that production processes consistently produce high quality products.
You may like: 14 Proven Health Tips for Men: Your Guide to a Healthier, Happier Life
Key Elements of Quality Control in Pharmaceutical Industry.
Quality Control in pharmaceutical industry is a comprehensive system that involves various elements to ensure that products meet required standards for safety, efficacy, and quality. Here are the key elements of this comprehensive system:
Raw Material Testing
One key element of quality control in pharmaceutical industry is raw material testing. This is done to ensure that raw materials used in production meet standard specifications, and do not contain toxic substances.
Below are what to look out for:
- Identification: Confirming the identity of raw materials before use. This is done to ensure that the materials are actually what they are said to be. For instance, more than one materials may have the same appearance. But both react differently when subjected to varies tests and conditions. By carrying out proper analysis on raw materials, we can confirm that they are what they are said to be, if not, the material is rejected and must not be used for production.
- Purity and Potency: Testing for contaminants and verifying the strength of active ingredients. This is crucial in QC. There are standards materials must meet before they are considered safe and fit for production. The potency (strength) of the raw materials must be withing a specified limit depending on the claim and pharmacopoeia used.
- Consistency: Ensuring uniformity in raw material batches. Quality control must ensure that the potency of raw materials fall withing specified limits, however, precision is more important than accuracy in this case. There should be consistency in the results of the potency of the materials, otherwise, an OOS or OOT document has to be raised.
All these are done using reliable equipment and chemicals where and when necessary.
In-Process Quality Control
A very important element of quality control is in-process control. They are in the process of manufacturing monitoring production processes, sampling and testing samples during production. All these to ensure quality and efficacy of the final product.
Here is what this element does:
- Monitoring Production: Continuous monitoring and control of manufacturing processes to ensure they operate within defined parameters. Any deviation is captured and corrected immediately.
- Sampling and Testing: Regular sampling and testing during production to detect any deviations from standards. If any deviation is detected at any point, it must be corrected before production can continue.
- Process Validation: Ensuring that manufacturing processes consistently produce products meeting predetermined quality criteria.
Finished Product Testing
After production, finished products are also tested before they are released to the market. This is to ensure that all production processes have been duly followed, and that the final product is of high quality.
These are what happen during finished products testing:
- Physical Tests: Assessing attributes such as weight, hardness, disintegration, friability and dissolution rates. These are confirmed using calibrated devices.
- Chemical Tests: Verifying the chemical composition and potency of the final product. This is also done using qualified equipment and reagents.
- Microbiological Tests: Testing for microbial contamination to ensure the product is free from harmful microorganisms. Suitable media are used for microbial analysis.
Stability Testing
Stability is a crucial element of quality control in pharmaceutical industry. Production is not complete if the product cannot be stable at a specified condition. This is why stability study is carried out on pharmaceutical products.
Here are what to test for:
- Shelf Life: Determining the product’s shelf life by testing it under various environmental conditions.
- Packaging Integrity: Ensuring that the packaging protects the product from environmental factors that could affect its quality.
Documentation and Records
Most pharmaceutical companies have a separate department outside quality control for this purpose. This unit or department is simply called documentation. It oversees everything that has to do with documentation and records.
Below is what this element of quality control does.
- Batch Records: Detailed records of each production batch, including raw materials used, process parameters, and test results. They also issue Batch Manufacturing Records (BMR) for production.
- Standard Operating Procedures (SOPs): Documented procedures for all QC activities to ensure consistency and compliance, as well as validity.
Equipment Calibration and Maintenance
Another important element of quality control in pharmaceutical industry is equipment calibration and maintenance. All qc processes are tested and validated. Every equipment used in each process is calibrated to ensure that every result gotten from any process is reliable.
Things to note:
- Calibration: Regular calibration of testing and measuring equipment to ensure accuracy.
- Preventive Maintenance: Routine maintenance of equipment to prevent malfunctions and ensure reliability.
Regulatory Compliance
Some companies have a different unit under quality. It ensures compliance to regulatory directives. These directives are there to ensure and enforce compliance to quality standards.
- Adherence to Guidelines: Complying with guidelines and standards set by regulatory authorities such as the FDA, EMA, NAFDAC, and WHO depending on region.
- GMP and GLP Compliance: Making sure that manufacturing processes comply with Good Manufacturing Practices (GMP) and Good Laboratory Practices.
Quality Audits
A good quality control component is quality audits which checks and confirm that quality protocols laid down by relevant regulatory bodies the country subscribe to are duly followed at each stage of the manufacturing and testing processes.
The two major quality audits are:
- Internal Audits: Regular audits conducted by internal teams to assess compliance with quality standards. This can be done inter-departmentally. That is, one department from the same organisation visits another department to check their processes for compliance.
- External Audits: Audits by regulatory authorities or third-party organisations to verify adherence to industry standards. After such audits, deviations noticed are categorised into three: minor, major, and critical depending on the weight of the deviation.
Quality Control Techniques and methods.
Due to the impacts pharmaceutical products have on patients’ health, Quality control is very important in this industry. To achieve the desired high quality products that meet patients’ needs, and at the same time comply with the standards set by the regulatory bodies, quality control employs many different techniques and methods.
Below are some quality control techniques and methods that help to ensure product quality and improvement overtime:
Statistical Control
Statistical quality (or process) control is a qc technique that makes use of statistical methods to monitor and control a process to ascertain that the processes under checks operate at their full potential. Such methods include control charts, and process sampling to detect variations and maintain quality throughout the production processes.
in Statistical Quality Control (SQC), using control charts and process sampling, a unit of the final product is sampled and tested first. This is to determine if the set standards for quality have been met or not. The sample size can be increased to represent more products.
This has what it tales to identify tolerable limits in product variations. Addition ally, it can result to discovering problems that will be addressed through corrective measures.
A quality control chart is a graph that manufacturers use to gauge how consistent their production quality is. this works by representing the number of defective products over time to identify patterns that can indicate whether the quantity of defects is constant, or if they fluctuate significantly, which can reveal issues in the production line. This allows organizations to fix those quality issues, be more productive.
Six Sigma
Six sigma is a quality control methodology that uses statistical methods to improve manufacturing process quality,and product quality. It achieves this by identifying and removing causes of defects and minimizing variability. It includes DMAIC (Define, Measure, Analyze, Improve, Control) and DMADV (Define, Measure, Analyze, Design, Verify) frameworks.
Inspection
Inspection (usually 100 per cent) inspection is a quality control method that thoroughly assesses all project items. In the case of 100% inspection, every single part of the processes is examined to ensure it meets quality standards.
Inspection can be:
- Visual Inspection where products are visually checked to identify defects or deviations.
- Instrumental Inspection where products are examined using instruments to check if they meet set standards.
Checklists
Quality Control uses checklists to control the monitoring of process inspections. It is used to ensure that every all necessary steps in a process inspection are completed. They also help in systematic verification and adherence to procedures.
Fishbone Diagram (Ishikawa Diagram)
This is a visual tool used in quality control to identify, explore, and display the possible causes of a specific problem or quality defect. This is optimally useful for root cause analysis.
Sampling
Sampling is a quality control method that is used to select part of a whole to determine whether or not the product or material meet predefined specifications.
Sampling can be:
- Random Sampling: As the name implies, samples are collected randomly from a lot for inspection. In this case, the samples collected represent the whole batch. After sampling, the samples are inspected and/or analysed using the necessary reagents, methods and equipment.
- Acceptance Sampling: This is a statistical measure that is used to determine whether or not a lot (batch) should be accepted or not based on a sample.
Six Sigma
Six Sigma is a set of techniques and tools used in quality control to ensure for process improvement. This method aims to reduce defects and variability. It uses the Define, Measure, Analyze, Improve, and Control (DMAIC) methodology.
Quality Management
This is a vital approach used to monitor and manage quality within an organisation. Quality management can be:
- Total Quality Management (TQM): This is a wide approach an organisation uses maintain to continuous improvement of all aspects of the business to meet or exceed customer expectations.
- Quality Management Systems (QMS): These are formalised systems that document processes, procedures, and responsibilities for achieving quality policies and objectives.
Failure Testing
Failure Testing is a method that involves testing a product until it fails. The product can be placed under different stresses such as humidity, vibration, temperature, etc until it fails.
Here are things to consider during failure testing:
- Stress Testing: This involves pushing a sample of a product beyond its normal operational capacity to ascertain its breaking point or stress limit.
- Failure Mode and Effects Analysis (FMEA): This is a systematic method that is used to evaluate processes to identify where and how they might fail and assessing the relative impact of different failures.
Process Control
Process control involves all statistical activities employed in quality control to check whether or not a particular process is reliable and predictable and results in a consistent performance with the least amount of variations. It can help to improve or control a process so that the desired results can be achieved.
Process control methods are of three types:
- Batch process control – In this method, exact quantities of particular raw materials are mixed for a precise period in a particular manner to achieve a specific product.
- Continuous process control – Here, variables remain the same throughout the process to produce the product at the best economy, maximum flow rate and given composition.
- Hybrid process control – In this method, elements of both continuous and batch process control can be included.
Quality Assurance (QA)
QA is a systematic process that determines whether or not products meet customers’ expectations. By preventing defects it focuses on improving processes used in manufacturing.
Histogram
A histogram is a graphical representation of data distribution. This method helps in understanding the underlying distribution of process data. It shows frequency of data points within specified ranges
Simply put, a histogram represents frequency distributions that indicate defects with bars.
Pareto Chart
Pareto principle states that 80% of problems are often due to 20% of causes. It is on this principle that Pareto chart finds its focus.
It is a bar graph that identifies the most significant factors in a dataset.
Stratification
This is a technique that is used to analyse the factors that affect the quality of the product. It is used to separate data gathered from various sources so that patterns can be identified.
Regulatory Standards and Guidelines
To ensure product efficacy and patient safety, regulatory bodies set strict regulatory standards and guidelines that pharmaceutical companies must adopt, follow and meet in all aspect of their processes. Failure to follow these guidelines can result to failed products. Such deviation can attract severe sanctions for the company.
Here are some key aspects and regulatory bodies involved:
Regulatory Bodies
FDA
Food and Drug Administration (FDA) has the role of overseeing the safety and efficacy of drugs, biological products, and medical devices in United State of America. The key Guidelines set out by FDA to control the quality of pharmaceutical products include: cGMP (Current Good Manufacturing Practice), CFR Title 21.
EMA
European Medicines Agency regulates medicines for human and veterinary use in EU. Some of the key Guidelines EMA oversees include: EU GMP (Good Manufacturing Practice), EudraLex – Volume 4.
WHO
World Health Organization (WHO) provides international standards and guidelines for pharmaceutical products. WHO key guidelines include: WHO GMP, WHO Guidelines on Good Distribution Practices (GDP).
ICH
International Council for Harmonisation of Technical Requirements for Pharmaceuticals for Human Use (ICH) ensure harmonisation of regulatory requirements across different regions. ICH key guidelines include: ICH Q7 (Good Manufacturing Practice for Active Pharmaceutical Ingredients), ICH Q10 (Pharmaceutical Quality System).
NAFDAC
National Agency for Food and Drug Administration and Control (NAFDAC) regulates and controls the manufacture, importation, exportation, distribution, advertisement, sale, and use of food, drugs, cosmetics, medical devices, packaged water, and chemicals in Nigeria.
NAFDAC key guidelines include: NAFDAC Good Manufacturing Practice (GMP) Guidelines, NAFDAC Guidelines for Registration of Pharmaceutical Products, NAFDAC Quality Assurance Guidelines.
Key Guidelines and Standards
Good Manufacturing Practices (GMP)
Good manufacturing practices is a guideline that ensures products are consistently produced and controlled according to quality standards. This guideline has several standards that several manufacturing processes must meet.
It covers all aspects of production: starting materials, premises, equipment, training, and personal hygiene of staff.
All pharmaceutical companies must abide by this guideline and ensure to meet the required standards for quality production of quality pharmaceutical products. Any deviation attracts sanctions depending on the strenght of the deviation: Minor, major or critical.
Good Laboratory Practices (GLP)
GLP is a guideline that ensures that good practices are adopted in laboratories. It ensures the consistency, reliability, reproducibility, quality, and integrity of chemical (including pharmaceuticals) non-clinical safety tests.
Good Distribution Practices (GDP)
GDP guides the quality and integrity of pharmaceutical products during all aspects of the distribution process.
Good Clinical Practices (GCP)
GCP is a quality control standard guides the designing, conducting, recording, and reporting clinical trials.
Pharmacopoeias
Pharmacopoeias are a compendiums of drug standards. They give guidelines on how each drug is tested, as well as the standards each active pharmaceutical ingredient present in the drug must meet.
Compendiums of drug standards include:
- USP (United States Pharmacopeia),
- EP (European Pharmacopoeia),
- JP (Japanese Pharmacopoeia),
- BP (British Pharmacopoeia).
- IP (Indian Pharmacopoeia), etc.
Quality by Design (QbD)
Quality by design is a systematic approach to development that begins with predefined objectives and emphasises product and process understanding and process control.
Risk Management
ICH Q9 provides principles and examples of tools for quality risk management that can be applied to different aspects of pharmaceutical quality.
Documentation and Record-Keeping
Standard Operating Procedures (SOPs)
SOPs are detailed, written instructions that guides every performer of actions on how to carry out the actions. This cut across manufacturing processes, equipment operation, analytical methods, etc. Some companies prefer to use Method of Analysis to refer to the same thing in analytical methods.
Batch Records
This is a detailed documentation of the entire production process for each batch of product.
Deviation Reports
This is a documentation of any deviations from established procedures or standards, including root cause analysis and corrective actions.
Audit Reports
This is a documentation of regular internal and external audits to ensure compliance with regulatory standards.
Roles of Quality Control Professionals
Quality control (QC) professionals play a critical role in the pharmaceutical industry. The roles of these professionals cannot be overemphasised. From ensuring that products meet regulatory standards and are safe, effective, and of high quality, to ensuring that pharmaceutical companies retain their positive reputations in the industry.
Their responsibilities are multifaceted and cover various aspects of the manufacturing process. Here are the key roles of QC professionals:
1. Testing and Analysis
- Sample Testing: QC professionals conduct physical, chemical, and microbiological testing of raw materials, in-process samples, and finished products to ensure they meet specified standards.
- Method Development: They develop, validate, and optimize analytical methods for testing products and materials.
- Stability Testing: They perform stability studies to determine the shelf life and storage conditions of products.
2. Documentation and Record-Keeping
- Accurate Records: Quality control professionals are trained to be able to maintain detailed and accurate records of all testing and analysis performed.
- Standard Operating Procedures (SOPs): They write, review, and update SOPs to ensure consistent and reliable QC processes.
- Batch Records: they also document the entire production process for each batch, including test results and deviations.
3. Compliance and Regulatory Affairs
- Regulatory Compliance: Although, this may be a different unit or department in various pharmaceutical companies, they ensure that all QC activities comply with local and international regulatory requirements (e.g., FDA, EMA, WHO, NAFDAC).
- Audit Preparation: They join heads with other departments or units in preparation for audits, and also participate in regulatory inspections and audits, providing necessary documentation and information.
- Quality Assurance (QA): Quality control collaborate with QA to implement and maintain quality management systems (QMS) and ensure overall compliance.
4. Process Control and Monitoring
- In-Process Control: Monitor and control manufacturing processes to ensure product quality throughout production.
- Critical Control Points: Identify and manage critical control points in the production process to prevent deviations and ensure consistent quality.
- Real-Time Monitoring: Utilize process analytical technology (PAT) for real-time monitoring and control of production processes.
5. Troubleshooting and Problem Solving
- Root Cause Analysis: Investigate and determine the root causes of deviations, out-of-specification (OOS) results, and other quality issues.
- Corrective and Preventive Actions (CAPA): Implement CAPA to address and prevent quality issues and improve processes.
6. Continuous Improvement
- Quality by Design (QbD): Apply QbD principles to enhance product and process understanding and improve quality.
- Process Optimization: Continuously review and optimize QC processes to increase efficiency and effectiveness.
- Innovation: Stay updated with the latest advancements in QC technologies and methodologies and implement them as appropriate.
7. Training and Development
- Staff Training: Train and mentor QC staff on testing methods, SOPs, regulatory requirements, and best practices.
- Continuous Education: Participate in ongoing professional development to keep abreast of industry trends and regulatory changes.
8. Risk Management
- Risk Assessment: Conduct risk assessments to identify and mitigate potential quality risks in the manufacturing process.
- Quality Risk Management (QRM): Implement QRM principles and tools to proactively manage quality risks.
9. Collaboration and Communication
- Cross-Functional Collaboration: Work closely with other departments such as manufacturing, R&D, and QA to ensure a cohesive approach to quality.
- Stakeholder Communication: Communicate QC findings and issues to relevant stakeholders, including management and regulatory bodies.
10. Environmental and Health Safety
- Safety Compliance: Ensure that QC activities comply with environmental and health safety regulations.
- Waste Management: Implement proper waste disposal methods for hazardous materials used in QC testing.
11. Technology and Automation
- Lab Automation: Utilize automated systems and technologies to increase the efficiency and accuracy of QC testing.
- Data Management Systems: Implement and manage electronic data management systems to ensure data integrity and accessibility.
12. Customer Focus
- Customer Complaints: Investigate and address customer complaints related to product quality.
- Product Release: Ensure that only products meeting all quality criteria are released to the market.
13. Pharmacovigilance Support
- Adverse Event Reporting: Support pharmacovigilance activities by providing QC data and analysis related to product safety.
- Post-Market Surveillance: Participate in post-market surveillance activities to monitor product quality and safety in the market.
14. Innovation and Development
- New Product Development: Collaborate with R&D during the development of new products to establish appropriate QC methods and specifications.
- Technology Transfer: Ensure smooth transfer of QC methods and processes from development to commercial production.
QC professionals are integral to ensuring that pharmaceutical products are safe, effective, and of high quality, playing a vital role in protecting public health and maintaining regulatory compliance.
Skills to Master as a Quality Control Personnel
To excel as a quality control (QC) professional in the pharmaceutical industry, mastering a diverse set of skills is essential. These skills ensure that QC personnel can effectively oversee the production process, maintain high-quality standards, and comply with regulatory requirements. Here are key skills to master:
1. Analytical Skills
- Laboratory Techniques: Proficiency in techniques such as chromatography (HPLC, GC), spectroscopy (UV, IR, NMR), and mass spectrometry.
- Microbiological Testing: Understanding microbiological methods and aseptic techniques for testing pharmaceutical products.
- Method Development and Validation: Ability to develop, validate, and optimize analytical methods for accurate testing.
2. Regulatory Knowledge
- GMP, GLP, GDP: Thorough knowledge of Good Manufacturing Practices, Good Laboratory Practices, and Good Distribution Practices.
- Regulatory Compliance: Familiarity with regulatory guidelines from bodies such as the FDA, EMA, WHO, NAFDAC, and ICH.
- Documentation Standards: Understanding of proper documentation practices, including SOPs, batch records, and audit trails.
3. Technical Skills
- Data Analysis: Proficiency in statistical tools and software for analyzing QC data (e.g., Minitab, SAS).
- Laboratory Information Management Systems (LIMS): Ability to use LIMS for managing laboratory data and workflows.
- Automation and Instrumentation: Knowledge of automated QC systems and instrumentation maintenance.
4. Attention to Detail
- Accuracy: Ensuring precise measurements and adherence to protocols.
- Observation: Keen eye for detecting deviations, anomalies, and non-conformances in processes and products.
5. Problem-Solving Skills
- Root Cause Analysis: Ability to identify the root causes of quality issues and implement corrective and preventive actions (CAPA).
- Troubleshooting: Skill in diagnosing and resolving issues with equipment, processes, and testing methods.
6. Project Management
- Planning and Organization: Effective management of multiple QC projects, prioritizing tasks, and meeting deadlines.
- Collaboration: Coordinating with cross-functional teams, including R&D, manufacturing, and quality assurance.
7. Communication Skills
- Technical Writing: Ability to write clear and concise reports, SOPs, and documentation.
- Interpersonal Communication: Strong verbal communication skills for interacting with team members, management, and regulatory auditors.
8. Critical Thinking
- Data Interpretation: Analyzing complex data sets and drawing accurate conclusions to guide decision-making.
- Risk Assessment: Evaluating potential risks and implementing strategies to mitigate them.
9. Continuous Learning and Adaptability
- Keeping Updated: Staying informed about industry trends, new technologies, and regulatory changes.
- Flexibility: Adapting to new methodologies, technologies, and changes in regulations.
10. Quality Management Systems (QMS)
- Implementation: Knowledge of QMS frameworks and their implementation in a pharmaceutical setting.
- Continuous Improvement: Using quality improvement tools and techniques such as Six Sigma, Lean, and Kaizen to enhance QC processes.
11. IT and Digital Skills
- Software Proficiency: Familiarity with software for data management, statistical analysis, and document control.
- Digital Transformation: Understanding the impact of digital technologies on QC processes, including AI and machine learning applications.
12. Ethical Conduct and Integrity
- Compliance: Adhering to ethical standards and regulatory requirements.
- Transparency: Maintaining honesty and transparency in all QC activities and reporting.
13. Environmental and Safety Awareness
- Safety Protocols: Knowledge of safety protocols for handling hazardous materials and maintaining a safe laboratory environment.
- Sustainability Practices: Understanding sustainable practices and their implementation in QC processes.
14. Interdisciplinary Knowledge
- Pharmaceutical Sciences: Basic understanding of pharmaceutical formulations, processes, and biopharmaceuticals.
- Engineering Principles: Knowledge of engineering principles relevant to pharmaceutical manufacturing and QC equipment.
15. Leadership and Mentorship
- Team Leadership: Ability to lead and motivate a QC team, fostering a culture of quality and continuous improvement.
- Mentorship: Providing guidance and training to junior QC staff, promoting professional development.
Mastering these skills will enable QC professionals to effectively oversee the quality of pharmaceutical products, ensuring compliance with regulatory standards and maintaining the highest levels of product safety and efficacy.
How to land high paying job as a quality control personnel
Landing a high-paying job as a quality control (QC) personnel in the pharmaceutical industry requires a combination of education, experience, skills, and strategic job-seeking tactics. Here are steps to help you achieve this goal:
1. Education and Certifications
- Advanced Degrees: Obtain a relevant degree in pharmaceutical sciences, chemistry, biochemistry, microbiology, or related fields. Consider pursuing a master’s or Ph.D. for higher-level positions.
- Certifications: Acquire certifications such as Certified Quality Auditor (CQA), Certified Quality Engineer (CQE), or Six Sigma certifications. These credentials can enhance your qualifications and demonstrate your commitment to quality.
- Regulatory Knowledge: Gain a thorough understanding of regulatory requirements and quality standards such as GMP, GLP, GDP, and ISO standards.
2. Relevant Experience
- Internships and Entry-Level Positions: Start with internships or entry-level positions in pharmaceutical or related industries to gain hands-on experience.
- Specialized Roles: Gain experience in specialized QC roles such as analytical chemistry, microbiology, validation, or regulatory compliance.
- Project Management: Lead or participate in projects that involve process improvement, method development, or new product introduction.
3. Skill Development
- Technical Skills: Master laboratory techniques, analytical methods, and instrumentation used in QC. Stay updated on advancements in QC technologies.
- Soft Skills: Develop strong communication, problem-solving, and critical thinking skills. Leadership and project management skills are also valuable.
- Continuous Learning: Participate in workshops, seminars, and training programs to stay current with industry trends and advancements.
4. Networking
- Professional Associations: Join professional organizations such as the American Society for Quality (ASQ), International Society for Pharmaceutical Engineering (ISPE), or the Parenteral Drug Association (PDA).
- Industry Conferences: Attend industry conferences, seminars, and workshops to network with professionals and stay updated on industry developments.
- LinkedIn: Build a strong LinkedIn profile, connect with industry professionals, and participate in relevant groups and discussions.
5. Job Search Strategies
- Targeted Job Search: Focus on companies known for high-paying QC positions, such as major pharmaceutical companies, biotechnology firms, and contract research organizations (CROs).
- Recruitment Agencies: Work with recruitment agencies that specialize in placing QC professionals in the pharmaceutical industry.
- Job Boards: Use specialized job boards such as PharmaOpportunities, BioSpace, and Indeed, and set up job alerts for QC positions.
6. Tailored Resume and Cover Letter
- Highlight Achievements: Emphasize your achievements, such as successful projects, process improvements, and compliance with regulatory standards.
- Keywords: Use industry-specific keywords to pass applicant tracking systems (ATS).
- Professional Formatting: Ensure your resume and cover letter are professionally formatted and free of errors.
7. Interview Preparation
- Research: Research the company and understand their products, processes, and quality standards.
- Practice: Practice answering common QC interview questions and prepare examples of your experience and accomplishments.
- Ask Questions: Prepare thoughtful questions about the company’s QC processes, challenges, and expectations.
8. Advanced Roles and Responsibilities
- Seek Leadership Roles: Aim for leadership or supervisory positions within the QC department to increase your earning potential.
- Cross-Functional Experience: Gain experience in related areas such as quality assurance (QA), regulatory affairs, and manufacturing to broaden your expertise and make you a more valuable asset.
9. Geographic Flexibility
- Location Matters: Be open to relocating to regions or cities where high-paying QC jobs are more prevalent, such as major pharmaceutical hubs.
10. Continuous Improvement
- Feedback: Seek feedback from supervisors and peers to continually improve your performance and skills.
- Professional Development: Stay committed to lifelong learning and professional development to advance your career.
By combining education, experience, and strategic job-seeking efforts, you can position yourself for a high-paying job as a QC professional in the pharmaceutical industry.
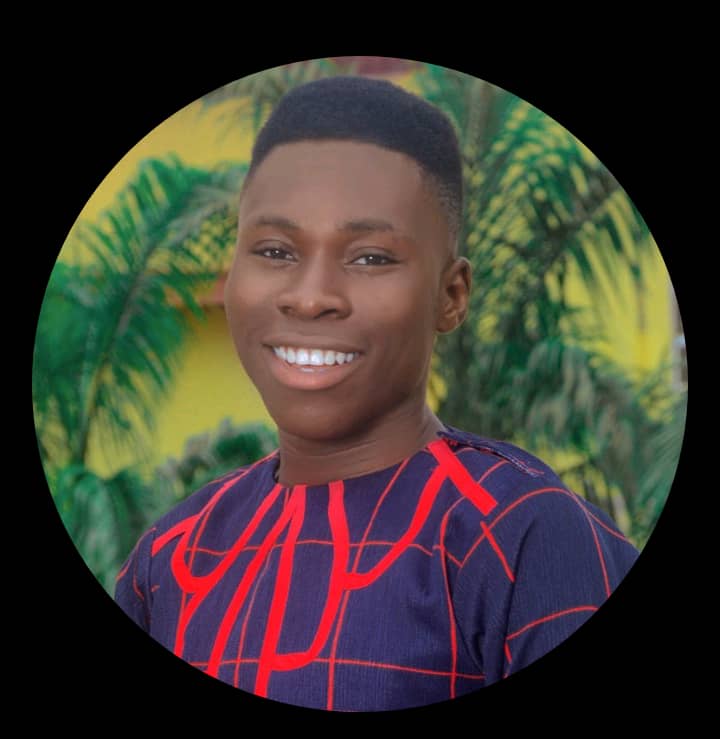
OKOLIE NWACHUKWU ANTHONY
Okolie Nwachukwu Anthony is a Biochemist, Writer, Blogger and Author known for his book “The Sorrowful Fall of The Risen Voiceless: Resilience and Bravery Against the Forces of Darkness.” He is the founder of PharmaFoodHealth.
In addition to his work as a writer, blogger and author, Okolie Nwachukwu Anthony is a Chemical Analyst and Quality Control Officer at Fidson Healthcare PLC. His professional roles involve ensuring that pharmaceutical products meet the necessary standards to safeguard the health of end users.